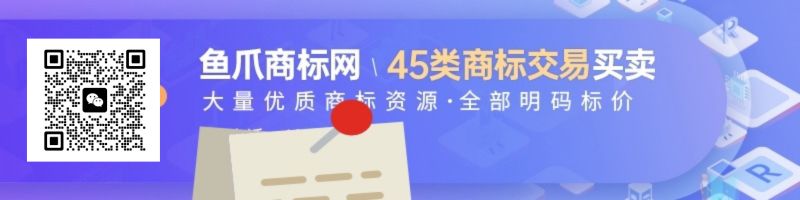
[0001]
本发明涉及一种模压加袋压一体成型工艺,具体涉及一种制作工艺简单,得到的性能稳定,强度高的复合材料椅背的模压加袋压一体成型工艺。
背景技术:
[0002]
复合材料目前已广泛应用于生产生活的各个
领域,复合材料还具有较高的强度和刚性、较好的抗冲击性,以及好的结构可设计性,有利于曲面结构的成型。复合材料不仅保持了各组分材料性能的优点,通过各组分的互补和关联,可以获得单一组成材料所不能达到的综合性能且易于成型,复合材料可以一体成型各种复杂形状。因此复合材料应用广泛,可应用于航空航天、医学、
汽车、
纺织和
机械制造等领域。目前复杂结构复合材料的成型一般采用将整体结构拆分成各个部件成型,然后再将各个部件粘接为整体产品。这种复杂结构复合材料的粘接方案存在以下问题:
[0003]
(1)、这种复杂结构复合材料产品的粘接方案,粘接后的产品强度过多依赖于粘接胶的强度,而远低于预浸料一体成型后得到的产品强度。
[0004]
(2)、这种复杂结构复合材料的产品的粘接方案工序复杂,对于批量性生产的产品来说耗时较多,生产
效率降低。
[0005]
(3)、这种复杂结构复合材料的产品的粘接方案,对于平面度要求比较高的产品,粘接操作难以满足平面度要求。
[0006]
(4)、这种复杂结构复合材料的产品的粘接方案,对于粘接组件配合度要求比较高的产品,粘接难以满足配合要求。
[0007]
(5)、这种复杂结构复合材料的产品的粘接方案,对于气密性要求比较高的产品,粘接部分容易漏气,难以满足气密性要求。
[0008]
(6)、这种复杂结构复合材料的产品的粘接方案,得到产品的粘接部分不耐高温及或其他湿热环境,使用时长较久时粘接胶强度降低有脱落风险。
技术实现要素:
[0009]
针对上述问题,本发明的主要目的在于提供一种制作工艺简单,得到的性能稳定,强度高的复合材料椅背的模压加袋压一体成型工艺。
[0010]
本发明是通过下述
技术方案来解决上述技术问题的:一种复合材料椅背的模压加袋压一体成型工艺,所述复合材料椅背的模压加袋压一体成型工艺包括如下步骤:
[0011]
步骤一:将复合材料椅背的整体复杂结构拆分成框架及面板两部分分别制作;
[0012]
步骤二:步骤一中的框架的制作工艺如下:框架采用预浸料料片铺贴完成,并预留的预浸料的料片翻边;
[0013]
步骤三:将步骤二中铺贴后的框架内置风管或硅胶管,并使用预留的料片翻边包裹风管或硅胶管,得到框架部分;
[0014]
步骤四:面板的制作工艺如下:采用预浸料料片按照图纸的大小裁切;
[0015]
步骤五:将步骤四中面板和步骤三中做好的已内置风管或硅胶管的框架的料片翻边部分进行搭接铺贴,得到完整产品预型体;
[0016]
步骤六:使用倒u型料片将端头风管或硅胶管进行防护,并锁紧气嘴;得到预成品;
[0017]
步骤七:应用模压加袋压工艺在步骤六中的预成品上后得到成品;
[0018]
步骤八:卸掉倒u型料片、风管或硅胶管。
[0019]
在本发明的具体实施例子中,所述步骤一中复合材料椅背中复杂结构包括曲面结构部分、弯折结构部分及凹槽部分和凸台部分。
[0020]
在本发明的具体实施例子中,所述步骤一中将复合材料椅背的整体复杂结构拆分成框架及面板两部分组成,将产品的复杂结构拆分出来具体包括以下步骤:
[0021]
根据复杂结构部分和产品的造型,考虑框架与面板结合的铺层方式、模具设计合理性、产品成型温度均匀、易脱模和易铺料因素设计复杂结构部分的模具和料片展形,根据产品强度、性能和外观要求,选取合适的预浸料片材,根据片材的厚度、克重、材料性能和面密度参数和产品重量要求设计复杂结构部分的工艺过程。
[0022]
在本发明的具体实施例子中,所述步骤二和三中拆分出来的框架单独铺贴完成并将料片翻边预留,并将铺贴后的框架内置风管或硅胶管,并使用预留的料片翻边包裹风管或硅胶管具体包括以下步骤:
[0023]
根据产品厚度要求及重量的分析结果,设计相匹配的预浸料料片展形,按照工艺设计的铺层顺序对预浸料料片进行铺层,所有预浸料料片尺寸均无需再手工剪裁,所有预浸料翻边进行预留后,内埋风管或软质硅胶管,然后使用预留的预浸料料片将风管或硅胶管完全包裹,得到框架部分。
[0024]
在本发明的具体实施例子中,所述步骤四拆分出来的面板与已包裹好风管或硅胶管的框架部分进行搭接铺贴,得到完整产品预型体具体包括以下步骤:
[0025]
根据产品造型及模具设计结构,将包裹好风管或硅胶管的框架部分模具镶块
定位完成,然后将面板部分预浸料与框架位置进行搭接,得到完整产品预型体。
[0026]
在本发明的具体实施例子中,所述步骤六中应用模压加袋压工艺一体成型得到成品具体包括以下步骤:
[0027]
根据主体模具设计要求,进行上下模合模,避免夹模情况下将模具放在硫化机上成型,加热工艺的温度为80~200℃;加热时间为30~120min;
[0028]
所述加压工艺的施压时间为30~120min;
[0029]
根据成型工艺和产品厚度的不同,需要不同的压力,加压工艺的压力范围为0.1~1mpa、1~2mpa或大于2mpa范围的一种;通过加热加压处理并保持30~120min,降温后取出,得到一体成型产品。
[0030]
在本发明的具体实施例子中,所述预浸料片材为碳纤维或芳纶增强的树脂预浸料片材中的一种。
[0031]
本发明的积极进步效果在于:本发明提供的复合材料椅背的模压加袋压一体成型工艺,在不使用除复合材料以外的其他辅助材料的情况下完成产品的制作,降低了生产成本及材料工艺复杂性;产品整体结构强度可满足在高冲击、高温等情况下的强度要求,通过本工艺制作的产品性能稳定,强度高。
附图说明
[0032]
图1-1为本发明的复合材料椅背的模压加袋压一体成型工艺的
流程图之一。
[0033]
图1-2为本发明的复合材料椅背的模压加袋压一体成型工艺的流程图之二。
[0034]
图1-3为本发明的复合材料椅背的模压加袋压一体成型工艺的流程图之三。
[0035]
图1-4为本发明的复合材料椅背的模压加袋压一体成型工艺的流程图之四。
[0036]
图2-1为本发明的复合材料椅背的整体结构正面
示意图。
[0037]
图2-2为本发明的复合材料椅背的整体结构侧面示意图。
[0038]
下面是本发明中标号对应的名称:
[0039]
框架1、面板2、风管或硅胶管3、曲面结构部分101、弯折结构部分102、凹槽部分103、凸台部分104、料片翻边105。
具体实施方式
[0040]
下面结合附图给出本发明较佳实施例,以详细说明本发明的技术方案。
[0041]
图1-1为本发明的复合材料椅背的模压加袋压一体成型工艺的流程图之一。图1-2为本发明的复合材料椅背的模压加袋压一体成型工艺的流程图之二。图1-3为本发明的复合材料椅背的模压加袋压一体成型工艺的流程图之三。图1-4为本发明的复合材料椅背的模压加袋压一体成型工艺的流程图之四。图2-1为本发明的复合材料椅背的整体结构正面示意图。图2-2为本发明的复合材料椅背的整体结构侧面示意图。如上述图所示:本发明提供的复合材料椅背的模压加袋压一体成型工艺,该复合材料椅背的模压加袋压一体成型工艺包括如下步骤:
[0042]
步骤一:将复合材料椅背的整体复杂结构拆分成框架1及面板2两部分分别制作;步骤一中复合材料椅背中复杂结构包括曲面结构部分101、弯折结构部分102及凹槽部分103和凸台部分104。
[0043]
步骤一中将复合材料椅背的整体复杂结构拆分成框架及面板两部分组成,将产品的复杂结构拆分出来具体包括以下步骤:
[0044]
根据复杂结构部分和产品的造型,考虑框架1与面板2结合的铺层方式、模具设计合理性、产品成型温度均匀、易脱模和易铺料因素设计复杂结构部分的模具和料片展形,根据产品强度、性能和外观要求,选取合适的预浸料片材,根据片材的厚度、克重、材料性能和面密度参数和产品重量要求设计复杂结构部分的工艺过程。
[0045]
步骤二:步骤一中的框架的制作工艺如下:框架采用预浸料料片铺贴完成,并预留的预浸料的料片翻边105;
[0046]
步骤三:将步骤二中铺贴后的框架内置风管或硅胶管3,并使用预留的料片翻边包裹风管或硅胶管,得到框架部分;
[0047]
步骤四:面板的制作工艺如下:采用预浸料料片按照图纸的大小裁切;
[0048]
步骤五:将步骤四中面板和步骤三中做好的已内置风管或硅胶管的框架的料片翻边105部分进行搭接铺贴,得到完整产品预型体;
[0049]
步骤六:使用倒u型料片将端头风管或硅胶管进行防护,并锁紧气嘴;得到预成品;
[0050]
步骤七:应用模压加袋压工艺在步骤六中的预成品上后得到成品;
[0051]
步骤八:卸掉倒u型料片、风管或硅胶管。
[0052]
步骤二和三中拆分出来的框架单独铺贴完成并将料片翻边预留,并将铺贴后的框架内置风管或硅胶管,并使用预留的料片翻边包裹风管或硅胶管具体包括以下步骤:根据产品厚度要求及重量的分析结果,设计相匹配的预浸料料片展形,按照工艺设计的铺层顺序对预浸料料片进行铺层,所有预浸料料片尺寸均无需再手工剪裁,所有预浸料翻边进行预留后,内埋风管或软质硅胶管,然后使用预留的预浸料料片将风管或硅胶管完全包裹,得到框架部分。
[0053]
步骤四拆分出来的面板2与已包裹好风管或硅胶管的框架部分进行搭接铺贴,得到完整产品预型体具体包括以下步骤:根据产品造型及模具设计结构,将包裹好风管或硅胶管的框架部分模具镶块定位完成,然后将面板部分预浸料与框架位置进行搭接,得到完整产品预型体。
[0054]
步骤六中应用模压加袋压工艺一体成型得到成品具体包括以下步骤:
[0055]
根据主体模具设计要求,进行上下模合模,避免夹模情况下将模具放在硫化机上成型,加热工艺的温度为80~200℃;加热时间为30~120min。
[0056]
根据成型工艺和产品厚度的不同,需要不同的压力,加压工艺的压力范围为0.1~1mpa、1~2mpa或大于2mpa范围的一种;通过加热加压处理并保持30~120min,降温后取出,得到一体成型产品。
[0057]
本发明中采用的预浸料片材为碳纤维或芳纶增强的树脂预浸料片材中的一种。
[0058]
下面是一个具体的实施例子:以连续碳纤维增强环氧树脂预浸料片材为原料,先进行产品框架部分预型,包裹风管或
乳胶管完成后,进行面板位置预型得到产品完整预型体,最终加压加热成型得到成品。具体的步骤如下:
[0059]
步骤一:根据复杂结构部分和产品的造型,考虑框架与面板结合的铺层方式、模具设计合理性、产品成型温度均匀、易脱模和易铺料因素设计复杂结构部分的模具和料片展形,根据产品强度、性能和外观等要求,选取合适的预浸料片材,根据片材的厚度、克重、材料性能和面密度参数和产品重量要求设计复杂结构部分的工艺过程。
[0060]
步骤二、三:根据产品厚度要求及重量的分析结果,设计相匹配的预浸料料片展形,按照工艺设计的铺层顺序对预浸料料片进行铺层,所有预浸料料片尺寸均无需再手工剪裁,所有预浸料翻边进行预留后,内埋风管或软质硅胶管,然后使用预留的预浸料料片将风管或硅胶管完全包裹,得到框架部分。
[0061]
步骤四:根据产品造型及模具设计结构,将包裹好风管或硅胶管的框架部分模具镶块定位完成,然后将面板部分预浸料与框架位置进行搭接,得到完整产品预型体。
[0062]
步骤五:根据产品厚度要求及重量的分析结果,将框架端头位置进行局部补强后,使用倒u型料片将风管或硅胶管进行包裹防护,保证风管包裹完全,降低漏气或爆袋风险,然后将气嘴使用扳手将其锁紧。
[0063]
步骤六:根据主体模具设计要求,进行上下模合模,避免夹模情况下将模具放在硫化机上成型,加热工艺的温度为80~200℃;加热时间为30~120min;
[0064]
所述加压工艺的施压时间为30~120min;
[0065]
根据成型工艺和产品厚度的不同,需要不同的压力,所述加压工艺的压力范围为0.1~1mpa、1~2mpa和大于2mpa范围的至少其中一种。通过加热加压处理并保持一段时间,降温后取出,得到一体成型产品。
[0066]
以上显示和描述了本发明的基本原理和主要特征和本发明的优点。本行业的技术人员应该了解,本发明不受上述实施例的限制,上述实施例和说明书中描述的只是说明本发明的原理,在不脱离本发明精神和范围的前提下,本发明还会有各种变化和改进,这些变化和改进都落入要求保护的本发明范围内,本发明要求保护范围由所附的权利要求书及其等效物界定。
如果您还有其他的疑问和需求,请点击【立即咨询】或者是添加微信号 【13608176338】
和我们鱼爪商标网客服取得联系,为你排忧解难! 此文章来源于网络,如有侵权,请联系删除
此文章来源于网络,如有侵权,请联系删除