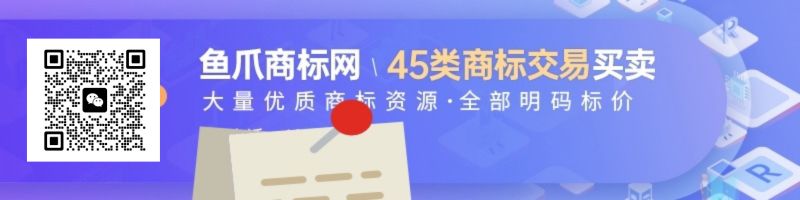
人造大理石3d薄壁壳体及其制备方法和应用
技术领域
[0001]
本发明涉及人造大理石技术领域,具体而言,涉及一种人造大理石3d薄壁壳体及其制备方法和应用。
背景技术:
[0002]
人造大理石有着天然美观的纹理以及冰凉的触感,有着特殊的附加值。传统的人造大理石通常为添加了大颗粒填料的热固性树脂基体体系。一般只能通过铸造或数控切割石料的方法实现人造大理石的3d造型,但是所制得的人造大理石产品的厚度非常厚(6mm以上),而且韧性差,容易脆碎。
[0003]
近年来,人造大理石材质的薄壁壳体引起了智能
手机后盖、平板
电脑后盖、
笔记本电脑外壳、智能穿戴设备外壳、无线充电器外壳、智能
家居产品外壳等领域的广泛关注。然而根据目前人造大理石加工方
法制得的产品的性能无法满足上述领域的需求。
技术实现要素:
[0004]
本发明的第一目的在于提供一种人造大理石3d薄壁壳体的制备方法,该方法解决了传统人造大理石厚度减薄有限、韧性差以及难以实现3d造型的技术问题,具有制备工艺简单、效率高等特点,且通过该方法制备的人造大理石3d薄壁壳体的厚度可以减薄到0.57mm。
[0005]
本发明第二目的在于提供一种所述的制备方法制得的人造大理石3d薄壁壳体,所述的人造大理石3d薄壁壳体具有韧性高、重量轻、厚度薄等优异性能。
[0006]
另外,本发明还提供了一种人造大理石3d薄壁壳体在智能
科技产品或
家具中的应用。
[0007]
为了实现本发明的上述目的,特采用以下技术方案:
[0008]
一种人造大理石3d薄壁壳体的制备方法,包括以下步骤:
[0009]
提供热塑性人造大理石板材,将所述热塑性人造大理石板材减薄至0.5mm~2.5mm;所述热塑性人造大理石板材的制备原料包括热塑性树脂基体及填料,所述填料为纳米级金属氢氧化物、纳米级金属氧化物、纳米级碳酸钙粉末、纳米级氮化物、硅微粉、
颜料、人造大理石碎料颗粒及树脂颗粒中的至少一种,所述热塑性树脂基体与所述填料的重量比例为3:7~2:3;
[0010]
将减薄后的产品预加热至130℃~250℃;
[0011]
提供冷压成型模具,将所述冷压成型模具加热至70℃~150℃,且所述冷压成型模具加热的温度低于所述热塑性人造大理石板材的预加热温度;
[0012]
将预加热后的热塑性人造大理石板材放置到所述冷压成型模具内冷压成型,脱模;
[0013]
将脱模后的产品与预浸料在20℃~90℃下进行热压复合。
[0014]
一种根据所述制备方法制得的人造大理石3d薄壁壳体。
[0015]
一种人造大理石3d薄壁壳体在智能科技产品或家具中的应用。
[0016]
与传统技术相比,本发明的有益效果为:
[0017]
(1)本发明中制备人造大理石3d薄壁壳体的方法,通过在树脂基体中添加合适的填料,可以使填料与热塑性树脂基体之间形成具有一定结合强度的界面,并且不会导致应力集中问题的产生,从而保证热塑性人造大理石板材在减薄过程中不会发生脆断。进一步选用热塑性的人造大理石板材结合冷压成型工艺,实现了人造大理石可以形成3d造型的目的。而通过增加纤维增强复合材料层,提高了人造大理石壳体的韧性。即本发明通过选用合适的原料和加工成型工艺解决了现有技术中人造大理石壳体难以实现3d造型以及厚度减薄受限和韧性差的技术问题。而且该方法还具有制备工艺简单,效率高的特点。
[0018]
(2)本发明制备的人造大理石3d薄壁壳体具有厚度薄,重量轻,韧性好的优异性能。传统人造大理石的厚度通常在6mm以上,而本发明制得的人造大理石3d薄壁壳体的厚度可以减薄到0.57mm。而且该壳体还拥有大理石外观纹理以及触感,非常适用于制作智能科技产品的外壳,例如手机后盖、平板电脑后盖、笔记本电脑外壳、智能穿戴设备外壳、无线充电器外壳等,还可以用于智能或传统家具产品的外壳等。
附图说明
[0019]
为了更清楚地说明本发明具体实施方式或现有技术中的技术方案,下面将对具体实施方式或现有技术描述中所需要使用的附图作简单地介绍,显而易见地,下面描述中的附图是本发明的一些实施方式,对于本领域普通技术人员来讲,在不付出创造性劳动的前提下,还可以根据这些附图获得其他的附图。
[0020]
图1为本发明制备的人造大理石3d薄壁壳体的立体示意图;
[0021]
图2为图1中人造大理石3d薄壁壳体的侧面剖视图。
具体实施方式
[0022]
现将详细地提供本发明实施方式的参考,其一个或多个实例描述于下文。提供每一实例作为解释而非限制本发明。实际上,对本领域技术人员而言,显而易见的是,可以对本发明进行多种修改和变化而不背离本发明的范围或精神。例如,作为一个实施方式的部分而说明或描述的特征可以用于另一实施方式中,来产生更进一步的实施方式。
[0023]
因此,旨在本发明覆盖落入所附权利要求的范围及其等同范围中的此类修改和变化。本发明的其它对象、特征和方面公开于以下详细描述中或从中是显而易见的。本领域普通技术人员应理解本讨论仅是示例性实施方式的描述,而非意在限制本发明更广阔的方面。
[0024]
本发明提供一种人造大理石3d薄壁壳体的制备方法,包括以下步骤:
[0025]
提供热塑性人造大理石板材,将所述热塑性人造大理石板材减薄至0.5mm~2.5mm;所述热塑性人造大理石板材的制备原料包括热塑性树脂基体及填料,所述填料为纳米级金属氢氧化物、纳米级金属氧化物、纳米级碳酸钙粉末、纳米级氮化物、硅微粉、颜料、人造大理石碎料颗粒及树脂颗粒中的至少一种,所述热塑性树脂基体与所述填料的重量比例为3:7~2:3;
[0026]
将减薄后的产品预加热至130℃~250℃;
[0027]
提供冷压成型模具,将所述冷压成型模具加热至70℃~150℃,且所述冷压成型模具加热的温度低于所述热塑性人造大理石板材的预加热温度;
[0028]
将预加热后的热塑性人造大理石板材放置到所述冷压成型模具内冷压成型,脱模;
[0029]
将脱模后的产品与预浸料在20℃~90℃下进行热压复合。
[0030]
本发明中制备人造大理石3d薄壁壳体的方法,通过在树脂基体中添加合适的填料,可以使填料与热塑性树脂基体之间形成具有一定结合强度的界面,并且不会导致应力集中问题的产生,从而保证热塑性人造大理石板材在减薄过程中不会发生脆断。进一步选用热塑性的人造大理石板材结合冷压成型工艺,实现了人造大理石可以形成3d造型的目的。而通过增加纤维增强复合材料层,提高了人造大理石壳体的韧性。即本发明通过选用合适的原料和加工成型工艺解决了现有技术中人造大理石壳体难以实现3d造型以及厚度减薄受限和韧性差的技术问题。而且该方法还具有制备工艺简单,效率高的特点。
[0031]
在本发明中,作为进一步说明,可以将热塑性人造大理石板材减薄至1mm、1.5mm、2mm。
[0032]
在本发明中,作为进一步说明,可以根据需要,在热塑性人造大理石板材的制备原料中添加色素或直接使用颜料作为着色剂。
[0033]
在本发明中,作为进一步说明,人造大理石碎料颗粒粒径为0.05mm~5mm。
[0034]
在本发明中,作为进一步说明,纳米级金属氢氧化物为纳米级氢氧化铝或纳米氢氧化镁;在一个优选的具体实施方式中,纳米级金属氢氧化物为纳米氢氧化铝。
[0035]
在本发明中,作为进一步说明,纳米级金属氧化物为纳米二氧化钛、纳米氧化铝或纳米氧化锌。
[0036]
在本发明中,作为进一步说明,纳米级氮化物为纳米氮化铝或纳米氮化硼。
[0037]
在本发明中,作为进一步说明,热塑性树脂基体为聚甲基丙烯酸酯及其改性树脂、聚丙烯树脂及其改性树脂、聚乙烯树脂及其改性树脂中的至少一种;在一个优选的具体实施方式中,热塑性树脂基体为聚甲基丙烯酸酯。
[0038]
在本发明中,作为进一步说明,预浸料为纤维增强树脂基体预浸料。
[0039]
在本发明中,作为进一步说明,预浸料中的树脂基体为环氧树脂、聚氨酯树脂、不饱和聚酯、聚乙烯树脂、聚丙烯树脂、聚碳酸酯、聚酰胺树脂及其改性树脂中的一种;在一个优选的具体实施方式中,预浸料中的树脂基体为环氧树脂。
[0040]
在本发明中,作为进一步说明,预浸料中的纤维为玻璃纤维、碳纤维、氧化铝纤维、聚丙烯纤维、聚乙烯纤维、芳纶纤维、亚麻纤维、玄武岩纤维及硼纤维中的至少一种;在一个优选的具体实施方式中,预浸料中的纤维为玻璃纤维。
[0041]
在本发明中,作为进一步说明,人造大理石3d薄壁壳体的制备方法还包括预浸料固化成型步骤。
[0042]
在本发明中,作为进一步说明,预浸料固化成型步骤可以与热塑性人造大理石板材和预浸料的复合步骤一步完成,也可以单独固化成型后再与热塑性人造大理石板材复合。
[0043]
在本发明中,作为进一步说明,预浸料固化成型后的厚度为0.07mm~1.5mm。
[0044]
在本发明中,作为进一步说明,在脱模后且在将脱模后的产品与预浸料进行热压
复合步骤之前还包括在脱模后的产品与预浸料之间引入胶粘层的步骤。
[0045]
在本发明中,作为进一步说明,胶粘层所用材料为聚氨酯热熔胶膜或聚氨酯胶粘剂。
[0046]
在本发明中,作为进一步说明,在脱模后且在将脱模后的产品与预浸料进行热压复合步骤之前还包括对脱模后的产品进行切割和研磨等。
[0047]
在本发明中,作为进一步说明,在脱模后的产品与预浸料进行热压复合步骤后还包括对所得热压复合后产品的切割和研磨等。
[0048]
在本发明中,作为进一步说明,冷压成型模具合模加压的压力为20t~60t,保压时间为1min~8min。
[0049]
在本发明中,作为进一步说明,减薄方法为水刀切割、激光切割、锯片切割、数控加工切割、研磨及抛光中的至少一种;在一个优选的具体实施方式中,减薄方法为数控加工切割和研磨。
[0050]
本发明还提供了一种根据制备方法制得的人造大理石3d薄壁壳体。
[0051]
本发明制备的人造大理石3d薄壁壳体具有厚度薄,重量轻,韧性好的优异性能。传统人造大理石的厚度通常在6mm以上,而本发明制得的人造大理石3d薄壁壳体的厚度可以减薄到0.57mm。而且该壳体还拥有大理石外观纹理以及触感,非常适用于制作智能科技产品的外壳,例如手机后盖、平板电脑后盖、笔记本电脑外壳、智能穿戴设备外壳、无线充电器外壳等,还可以用于智能或传统家具产品的外壳等。
[0052]
本发明进一步提供了一种人造大理石3d薄壁壳体在智能科技产品和家具中的应用。
[0053]
在本发明中,作为进一步说明,所述智能科技产品包括
智能手机、平板电脑、笔记本电脑、智能穿戴设备、无线充电器、智能家居产品。
[0054]
下面将结合实施例对本发明的实施方案进行详细描述。
[0055]
实施例1
[0056]
通过对含有重量比例为3:7的聚甲基丙烯酸酯基体和纳米氢氧化铝填料的热塑性人造大理石板材进行数控加工切割和研磨减薄至0.6mm。将减薄后的热塑性人造大理石板材在160℃下进行预加热。对冷压成型模具加热至100℃,并保持恒温。随后将预加热后的热塑性人造大理石板材放置到冷压成型模具的模腔内,合模加压至60t,并对模具进行保压3min。保压结束后脱模,所得脱模产品在室温下自然冷却后进行切割,去除毛边得人造大理石3d薄壁壳体中间产品。然后将人造大理石3d薄壁壳体中间产品与玻璃纤维增强环氧树脂基体的预浸料在50℃下进行热压复合。最终对热压复合后的样品进行数控加工切割、研磨即得0.85mm的人造大理石3d薄壁壳体。
[0057]
分别选用厚度为0.85mm的本实施例制备的人造大理石3d薄壁壳体与无纤维增强复合材料层的人造大理石薄板平片进行抗冲击测试。测试结果为:选用110g的钢球在50cm的高度落球冲击无纤维增强复合材料层的人造大理石薄板平片,产品碎裂;而选用1kg的钢球在1m的高度落球冲击本实施例制备的人造大理石3d薄壁壳体,产品无开裂。说明通过本发明中制备方法制备的人造大理石3d薄壁壳体的抗冲击强度高,具有很好的韧性。
[0058]
实施例2
[0059]
通过对含有重量比例为3:7的聚甲基丙烯酸酯基体和纳米氢氧化铝填料的热塑性
人造大理石板材进行切割和研磨减薄至2.0mm。将减薄后的热塑性人造大理石板材在190℃下进行预加热。对冷压成型模具加热至100℃,并保持恒温。然后按照设定的叠层的方式,将玻璃纤维增强环氧树脂基体的预浸料与热塑性人造大理石板材一同放入冷压成型模具的模腔内,合模加压至20t,并对模具进行保压120min。保压结束后脱模,所得脱模产品在室温下自然冷却后进行切割、抛光,去除毛边得人造大理石3d薄壁壳体。
[0060]
实施例3
[0061]
通过对含有重量比例为3:7的聚甲基丙烯酸酯基体和纳米氢氧化铝填料的热塑性人造大理石板材进行切割和研磨减薄至1.1mm。将减薄后的热塑性人造大理石板材在150℃下进行预加热。对冷压成型模具加热至100℃,并保持恒温。随后将预加热后的热塑性人造大理石板材放置到冷压成型模具的模腔内,合模加压至60t,并对模具进行保压3min。保压结束后脱模,所得脱模产品在室温下自然冷却后进行切割,去除毛边得人造大理石3d薄壁壳体中间产品。将玻璃纤维增强环氧树脂基体的预浸料在120℃和15t压力下单独固化30min后得纤维增强复合材料层。然后人造大理石3d薄壁壳体中间产品与复合材料层在105℃和1t压力下通过聚氨酯热熔胶膜粘结而成。对所得最终产品进行切割、抛光,去除毛边得人造大理石3d薄壁壳体。
[0062]
实施例4
[0063]
通过对含有重量比例为3:7的聚甲基丙烯酸酯基体和纳米氢氧化铝填料的热塑性人造大理石板材进行切割和研磨减薄至1.0mm。将减薄后的热塑性人造大理石板材在150℃下进行预加热。对冷压成型模具加热至95℃,并保持恒温。随后将预加热后的热塑性人造大理石板材放置到冷压成型模具的模腔内,合模加压至30t,并对模具进行保压3min。保压结束后脱模,所得脱模产品在室温下自然冷却后进行切割,去除毛边得人造大理石3d薄壁壳体中间产品。将玻璃纤维增强环氧树脂基体的预浸料在120℃和15t压力下单独固化30min后得纤维增强复合材料层。然后将人造大理石3d薄壁壳体中间产品与复合材料层在90℃和200kg压力下通过聚氨酯胶粘剂粘接在一起。对所得最终产品进行切割、抛光,去除毛边得人造大理石3d薄壁壳体。
[0064]
实施例5
[0065]
通过对含有重量比例为3:7的聚甲基丙烯酸酯基体和纳米氢氧化铝填料以及含有0.1%色素的热塑性人造大理石板材进行切割和研磨减薄至0.5mm。将减薄后的热塑性人造大理石板材在160℃下进行预加热。对冷压成型模具加热至90℃,并保持恒温。随后将预加热后的热塑性人造大理石板材放置到冷压成型模具的模腔内,合模加压至30t,并对模具进行保压3min。保压结束后脱模,所得脱模产品在室温下自然冷却后进行切割,去除毛边得人造大理石3d薄壁壳体中间产品。然后将人造大理石3d薄壁壳体中间产品与玻璃纤维增强环氧树脂基体的预浸料在50℃下进行热压复合。最终对热压复合后的样品进行切割、研磨即得人造大理石3d薄壁壳体。
[0066]
实施例6
[0067]
通过对含有重量比例为2:1:2的聚丙烯基体、纳米氢氧化铝和纳米氢氧化镁填料的热塑性人造大理石板材进行切割和研磨减薄至2mm。将减薄后的热塑性人造大理石板材在190℃下进行预加热。对冷压成型模具加热至100℃,并保持恒温。随后将预加热后的热塑性人造大理石板材放置到冷压成型模具的模腔内,合模加压至20t,并对模具进行保压
3min。保压结束后脱模,所得脱模产品在室温下自然冷却后进行切割,去除毛边得人造大理石3d薄壁壳体中间产品。然后将人造大理石3d薄壁壳体中间产品与玻璃纤维增强水性聚氨酯粘合剂层在90℃下进行热压复合。最终对热压复合后的样品进行切割、研磨即得人造大理石3d薄壁壳体。
[0068]
对实施例2~6所得人造大理石3d薄壁壳体进行抗冲击性能测试,得到的测试结果与实施例1相近,说明本发明制备的人造大理石3d薄壁壳体具有优异的韧性。
[0069]
本发明制备的人造大理石3d薄壁壳体的立体示意图如图1所示,图中人造大理石3d薄壁壳体10的结构如图2所示。人造大理石3d薄壁壳体10包括人造大理石3d薄壁壳体外壁11和纤维增强复合材料层12。
[0070]
以上所述实施例的各技术特征可以进行任意的组合,为使描述简洁,未对上述实施例中的各个技术特征所有可能的组合都进行描述,然而,只要这些技术特征的组合不存在矛盾,都应当认为是本说明书记载的范围。
[0071]
以上所述实施例仅表达了本发明的几种实施方式,其描述较为具体和详细,但并不能因此而理解为对发明
专利范围的限制。应当指出的是,对于本领域的普通技术人员来说,在不脱离本发明构思的前提下,还可以做出若干变形和改进,这些都属于本发明的保护范围。因此,本发明专利的保护范围应以所附权利要求为准。
如果您还有其他的疑问和需求,请点击【立即咨询】或者是添加微信号 【13608176338】
和我们鱼爪商标网客服取得联系,为你排忧解难! 此文章来源于网络,如有侵权,请联系删除
此文章来源于网络,如有侵权,请联系删除