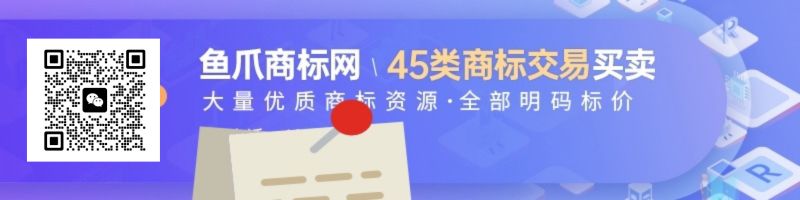
[0001]
本发明涉及热管理材料技术
领域,尤其是涉及导热复合材料及其制备方法和应用。
背景技术:
[0002]
随着
电子科技的迅猛发展以及5g通讯、物联网、新
能源汽车电子、智能可穿戴设备等领域的不断兴起,相关电子器件的功率密度和集成度日益提高。电子器件工作时,部分的功率损耗以热量向外导出,而电子器件的耗散发热会直接导致电子设备温度的快速上升和热应力增加,对电子器件的工作可靠性、安全性和使用寿命造成严重威胁。这也使得业界人士逐渐认识到,导热材料技艺能否突破在一定程度上决定了电子器件能否更进一步发展。
[0003]
出于电子器件的长期稳定性的考虑,导热材料不仅对导热系数有要求,其
机械强度、电绝缘等性能也必须满足一定标准。高分子聚合物因其良好的电气绝缘性能、耐腐蚀、易加工、机械强度高等特点成为了目前应用最广的一种导热材料。然而,大部分聚合物的热导率都很低,使用时往往以聚合物材料作为基体,在其中添加高导热填料来增加导热复合材料的热导率。
[0004]
目前大多需要较高的填料比例才能获得较高的导热性能。但是,由于导热填料和聚合物基体两者不相容,导热填料添加量的增加会导致复合材料的粘度增大、成型性能和力学性能下降。研究人员因而尝试选择一些具有优良导热性能的材料作为填料使用。例如六方氮化硼(hbn)、片层状石墨或石墨烯等的二维导热材料的面内方向的导热系数可达数百w/m
·
k,其优异的导热性在导热复合材料方面有广阔的应用前景,但现有技术无法充分利用其各向异性的性能,以实现导热复合材料的热导率最大化,而这也制约了二维材料在导热复合材料中的应用。因此,有必要提供一种有效提高热导率的导热复合材料的制备方法。
技术实现要素:
[0005]
本发明旨在至少解决现有技术中存在的技术问题之一。为此,本发明提出一种能够有效提高导热性能的导热复合材料的制备方法、该制备方
法制备得到的导热复合材料和该导热复合材料的应用。
[0006]
第一方面,本发明的一个实施例提供了一种导热复合材料的制备方法,该制备方法包括以下步骤:
[0007]
s1:填料和聚合物基体混合得到浆料;
[0008]
s2:将浆料通过薄膜成型工艺制成第一复合膜;
[0009]
s3:将第一复合膜卷绕,形成第一柱体;
[0010]
s4:将第一柱体通过所述薄膜成型工艺制成第二复合膜,卷绕后形成第二柱体;
[0011]
s5:将第二柱体加压固化成型;
[0012]
填料包括二维导热片材。
[0013]
本发明实施例的导热复合材料的制备方法至少具有如下有益效果:
[0014]
本发明实施例通过薄膜卷曲后加压成型的方式制备高导热复合材料,形成薄膜的过程中所采用的二维导热片材在压力和/或剪切力的作用下沿薄膜平面方向排列,利用卷曲工艺加压成型,在压力作用下进一步提高薄膜取向,并且通过卷曲和挤出步骤的重复来强化加压所造成的压力影响,使其中的二维导热片材尽可能地取向,充分利用二维导热片材的各向异性的导热性能,获得更高的热导率。
[0015]
显然,为了使卷曲和挤出所需要的强化作用以尽可能地高效叠加,前后不同轮次的薄膜成型和卷绕拟达成的二维导热片材的取向方向(压力和/或剪切力对于材料的作用方向)相同、或者至少相近;以避免前后取向方向不同而导致固化成型后的导热复合材料因其中的二维导热片材相互交叉而削弱其导热性能。
[0016]
根据本发明的一些实施例的制备方法,进行s5前,重复s4两到三次。重复s4的挤出和卷曲两到三次可以最大程度地强化压力影响,最大化二维导热片材的取向。
[0017]
根据本发明的一些实施例的制备方法,s5后还包括s6:加压固化成型后,沿垂直于第二柱体的轴向的方向切割,得到片状导热复合材料。通过该方法获得的片状导热复合材料在垂直于片状平面的方向上取向,具有良好的热导率。
[0018]
根据本发明的一些实施例的制备方法,填料还包括球形导热粉体。球形导热粉体的球形度越高,其表面能就越小,粉体的表面流动性就越好,从而越能够确保填料和聚合物基体的良好结合,也就越能够有效减少对浆料体系粘度的影响。同时,表面流动性越好,在挤出成膜时越可能将压力和/或剪切力更好地作用到填料上,二维导热片材在其中的转动阻力就越小,取向的效果也就越好。
[0019]
根据本发明的一些实施例的制备方法,球形导热粉体选自球形二氧化硅、球形氮化铝、球形氧化铝中的至少一种。
[0020]
根据本发明的一些实施例的制备方法,球形导热粉体为球形氧化铝。球形二氧化硅、球形氮化硼在提高流动性方面效果较好,但球形二氧化硅的热导率较差,球形氮化铝的热导率虽高,但容易水解生成氢氧化铝和氨气而影响其作为导热填料的正常使用。因此,球形导热粉体优选兼具热导率和稳定性的球形氧化铝。
[0021]
根据本发明的一些实施例的制备方法,基于浆料的总质量,二维导热片材的质量分数为5~30%,球形导热粉体的质量分数为5~80%。
[0022]
根据本发明的一些实施例的制备方法,填料经表面改性处理;优选地,表面改性处理的方法选自化学接枝、超声、微波、紫外、酸处理、碱处理中的至少一种。通过表面改性处理提高导热填料和聚合物基体之间的相容性,使两者形成更有效的热量传递,从而提高复合材料的热导率。偶联剂处理的方式可以是采用包括但不限于硅烷偶联剂、钛酸酯类偶联剂、铝酸酯类偶联剂等偶联剂对导热填料进行处理。或者通过超声、微波、紫外、酸处理、碱处理等方式在导热填料的表面形成疏水基团,从而使导热填料更容易被聚合物基体润湿,提高复合材料的热导率。
[0023]
根据本发明的一些实施例的制备方法,薄膜成型工艺选自流延工艺、压延工艺、拉伸工艺、刮涂工艺中的任一种。其中,第一次形成第一复合膜和第二次形成第二复合膜以及s4的可能的重复过程等不同工序所采用的具体的薄膜成型工艺可以相同或不同,例如,可以第一次流延、第二次压延;第一次流延、第二次压延;第一次压延、第二次压延;第一次拉
伸,第二次刮涂等。
[0024]
根据本发明的一些实施例的制备方法,流延工艺或压延工艺可以采用包括流延机、刮涂机、膜压机、三辊压延机等在内的设备利用压力和/或剪切力成膜。
[0025]
根据本发明的一些实施例的制备方法,二维导热片材选自六方氮化硼、片层状石墨、石墨烯中的一种或多种。
[0026]
根据本发明的一些实施例的制备方法,聚合物基体包括有机硅、聚氨酯、丙烯酸、聚乙烯、聚乙烯醇、环氧树脂、聚酰亚胺等其中的至少一种。其中,有机硅可以是诸如硅油、硅
橡胶等有机硅聚合物。
[0027]
根据本发明的一些实施例的制备方法,形成第一柱体和/或形成第二柱体的方式可以是将第一复合膜和/或第二复合膜沿其侧面卷绕形成圆柱形材料。为了保证层与层之间热量传递效率,卷绕应使各层之间紧密贴合。
[0028]
第二方面,本发明的一个实施例提供了一种导热复合材料,该导热复合材料采用上述的制备方法制得。
[0029]
本发明实施例的导热复合材料至少具有如下有益效果:
[0030]
本发明实施例通过上述方法制备得到的高导热复合材料在形成薄膜的过程中的二维导热片材受压力和/或剪切力的影响下沿薄膜平面方向排列,通过卷曲和挤出步骤的重复来强化加压固化成型时加压的影响,导热复合材料中的二维导热片材取向程度较高,因而相比于现有的导热材料而言,具有更高的热导率。
[0031]
第三方面,本发明的一个实施例提供了一种电子器件,该电子器件包括上述的导热复合材料。
[0032]
本发明实施例的电子器件至少具有如下有益效果:
[0033]
电子器件中采用上述的导热复合材料进行散热或辅助散热。由于该导热复合材料具有较高的导热率,在电子器件中使用可以将产生的热量高效快捷地传递除去,有效减缓电子器件的温度升高,提高长期工作条件下电子器件的工作可靠性、安全性和使用寿命。
附图说明
[0034]
图1~图4是本发明的实施例1的导热复合材料的制备方法的流程示意图。
具体实施方式
[0035]
以下将结合实施例对本发明的构思及产生的技术效果进行清楚、完整地描述,以充分
地理解本发明的目的、特征和效果。显然,所描述的实施例只是本发明的一部分实施例,而不是全部实施例,基于本发明的实施例,本领域的技术人员在不付出创造性劳动的前提下所获得的其他实施例,均属于本发明保护的范围。
[0036]
实施例1
[0037]
本实施例提供一种导热复合材料及其制备方法,图1~图4是本发明的实施例1的导热复合材料的制备方法的流程示意图。参考图1~图4,该导热复合材料的制备方法包括以下步骤:
[0038]
填料预处理:15质量份的石墨烯和60质量份的球形氧化铝粉末混合后使用偶联剂kh550进行改性处理,得到改性填料。
[0039]
s1:将改性填料与25质量份的聚乙烯醇混合均匀形成浆料。
[0040]
s2:参考图1,通过压延工艺将浆料形成如图1的第一复合膜100。
[0041]
s3:参考图2,将第一复合膜100沿侧面卷绕,形成紧密贴合的第一圆柱体。
[0042]
s4:将第一圆柱体通过压延工艺形成第二复合膜,将第二复合膜沿侧面卷绕,形成紧密贴合的第二圆柱体;将第二圆柱体通过压延工艺形成第三复合膜,将第三复合膜沿侧面卷绕,形成紧密贴合的第三圆柱体。
[0043]
s5:参考图3中箭头所示方向,将第三圆柱体300放入长方体模具310中,其中,长方体模具310的侧面为正方形,正方形的边长d1小于第三圆柱体300的直径d2,加压固化成型。
[0044]
s6:参考图4,成型后的材料400使用切割刀具410沿垂直于轴向的方向切割,得到片状导热复合材料。
[0045]
实施例2
[0046]
本实施例提供一种导热复合材料,与实施例1的区别在于,采用超声和偶联剂kh560处理后的20质量份的六方氮化硼与60质量份的球形氧化铝粉末作为填料,以20质量份的硅油作为聚合物基体。该导热复合材料的制备方法与实施例1相同。
[0047]
实施例3
[0048]
本实施例提供一种导热复合材料,与实施例1的区别在于,采用化学接枝端氨基聚硅氧烷的20质量份的片层状石墨与70质量份的球形氧化铝粉末作为填料,以10质量份的硅油作为聚合物基体。材料制备步骤与实施例1相同。
[0049]
对比实验
[0050]
对比例1
[0051]
该对比例提供一种导热复合材料,与实施例1的区别在于,未加入偶联剂进行改性。同时,在制备过程中,与实施例1的区别在于,将浆料直接压延成型得到导热复合材料。
[0052]
对比例2
[0053]
该对比例提供一种导热复合材料,与实施例2的区别在于,制备过程中将浆料直接压延成型得到导热复合材料。
[0054]
对比例3
[0055]
该对比例提供一种导热复合材料,与实施例3的区别在于,制备方法不同,具体步骤如下:
[0056]
填料预处理:20质量份的片层状石墨与70质量份的球形氧化铝粉末混合后使用端氨基聚硅氧烷进行表面改性处理,得到改性填料。
[0057]
步骤1:将改性填料与10质量份的硅油混合均匀形成浆料。
[0058]
步骤2:通过压延工艺将浆料形成第一复合膜。
[0059]
步骤3:将第一复合膜沿侧面卷绕,形成紧密贴合的第一圆柱体。
[0060]
步骤4:将第一圆柱体放入两端边长小于第三圆柱体直径的长方形模具中,加压固化成型。
[0061]
步骤5:成型后的材料沿第一圆柱体的轴向的方向切割,得到片状导热复合材料。
[0062]
采用稳态平面热源法测定片状导热复合材料沿二维导热片材的取向方向的导热率,测试的具体方法为:按照astm5470-06标准,将导热复合材料放置于电阻电导率测量仪的高温段、低温段之间,建立稳定的热流后,测量冷热端的温度差,从而确定片状导热复合
材料沿平行于图4轴向的热导率。
[0063]
分别将实施例1~3以及对比例1~3中制得的片状导热复合材料按照上述方法测定其热导率,结果如表1。
[0064]
表1.热导率测定结果
[0065] 实施例1实施例2实施例3对比例1对比例2对比例3热导率(w/m
·
k)6.75.44.91.92.63.1
[0066]
从上述结果可以看出,对比例1相对于实施例1并未对导热填料进行改性处理,同时采用直接压延成型的方式,这导致对比例1的热导率不足实施例1的三分之一;对比例2相对于实施例2直接成型而没有采用多次卷曲成膜后加压成型的方式,使其热导率仅有实施例2的一半不到。实施例3中通过经过多次卷曲成膜的方式加压固化成型,相对于对比例3在一次卷曲成膜后直接加压固化成型,热导率提升了约60%。可见,通过卷曲和挤出步骤的重复来强化加压所造成的压力影响,使其中的二维导热片材尽可能地取向,能够充分利用二维导热片材的各向异性的导热性能,使得导热复合材料获得更高的热导率。
[0067]
实施例4
[0068]
本实施例提供一种电子器件,该电子器件包括依次设置的芯片和
散热器,芯片和散热器之间夹设有热传递粘合剂,该热传递粘合剂包括实施例1的导热复合材料。利用该导热复合材料,芯片在工作中产生的热量可以迅速传递到散热器从而耗散出去,有效减缓芯片的温升,避免温度过高导致工作可靠性、安全性和使用寿命的下降。
[0069]
上面结合实施例对本发明作了详细说明,但是本发明不限于上述实施例,在所述技术领域普通技术人员所具备的知识范围内,还可以在不脱离本发明宗旨的前提下作出各种变化。此外,在不冲突的情况下,本发明的实施例及实施例中的特征可以相互组合。
如果您还有其他的疑问和需求,请点击【立即咨询】或者是添加微信号 【13608176338】
和我们鱼爪商标网客服取得联系,为你排忧解难! 此文章来源于网络,如有侵权,请联系删除
此文章来源于网络,如有侵权,请联系删除